The Role of Modern Technology in Modern Welding Inspection Madison Practices
The Role of Modern Technology in Modern Welding Inspection Madison Practices
Blog Article
The Value of Thorough Welding Assessment in Industrial Applications
In the world of industrial applications, the importance of meticulous welding assessment can not be overemphasized. As we discover the multifaceted advantages of attentive welding examinations, one have to think about the broader implications on safety and security, dependability, and cost-effectiveness in industrial procedures.
Enhancing Architectural Integrity
When it comes to welding assessment in industrial applications, improving architectural honesty is critical. The key goal of welding evaluation is to ensure that the welds can bearing the anticipated lots and tensions they will run into in solution. This includes an extensive analysis of the welds' dimensions, positioning, and overall quality, ensuring they fulfill the defined codes and standards. Accurate examination approaches, such as aesthetic evaluation, ultrasonic testing, and radiographic screening, are essential in identifying issues that can jeopardize the framework's safety and capability - Welding Inspection Madison.
The significance of keeping architectural honesty in bonded structures can not be overstated. Poorly implemented welds can lead to devastating failures, leading to pricey fixings, downtime, and also endangerment of human lives. Assessors play a vital role in the lifecycle of industrial elements, offering assurance that the welding procedure delivers the wanted toughness and toughness.
Moreover, advanced modern technologies, such as phased selection ultrasonic screening and digital radiography, deal improved abilities in detecting possible weak points, enabling corrective steps before problems intensify. By prioritizing the stability of welds with meticulous inspection, industries can make sure functional performance and expand the durability of their facilities.
Identifying Welding Problems
Recognizing welding issues is a critical element of making certain the safety and security and integrity of bonded structures. These defects can compromise the honesty of the entire assembly and, if left unaddressed, may cause devastating failures. Usual welding defects consist of porosity, fractures, insufficient fusion, and damaging. Each of these defects occurs from specific reasons, such as inappropriate welding methods, contamination, or insufficient warmth control.

Competent examiners make use of both aesthetic evaluation and progressed non-destructive testing (NDT) techniques, such as ultrasonic or radiographic testing, to find these flaws. The timely identification and rectification of welding defects are vital to keep the structural integrity and long life of industrial elements.
Making Certain Compliance Specifications
Keeping the honesty of welded frameworks expands past identifying flaws; it requires adherence to strict conformity standards. Compliance with well-known standards, such as those offered by the American Welding Society (AWS) and the International Company for Standardization (ISO), makes certain that welds fulfill minimum safety and top quality requirements. These standards encompass a vast range of criteria, consisting of product requirements, welding treatments, and certification of welders. Adherence to these criteria is essential to avoid architectural failings, which might lead to catastrophic consequences in commercial applications.
Normal audits and examinations are important in verifying compliance. Assessors must have a detailed understanding of the relevant requirements and be skilled at making use of numerous non-destructive testing (NDT) methods to assess weld top quality. By making certain that welding techniques straighten with compliance standards, companies minimize the danger of non-conformity, which can lead to legal obligations and safety and security threats.
Additionally, maintaining conformity not just safeguards architectural stability but additionally improves a company's credibility in the industry. Stakeholders and customers are more probable to trust fund firms that continually demonstrate a commitment to top quality and safety via strenuous compliance. Hence, making certain conformity standards is a crucial part in the successful implementation of welding in commercial applications.
Lowering Maintenance Costs
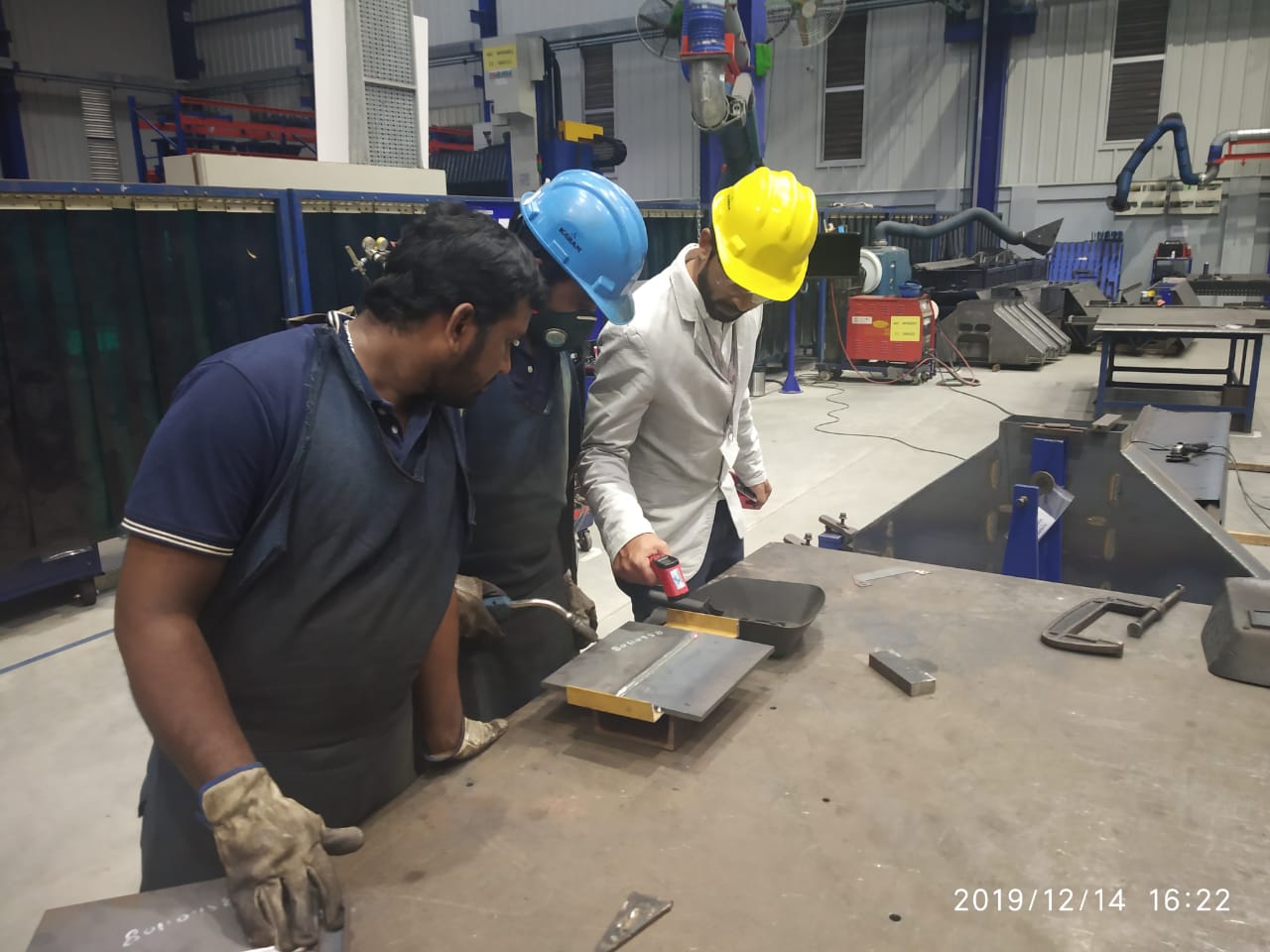
The application of advanced non-destructive testing (NDT) methods, including ultrasonic, radiographic, and magnetic bit evaluations, improves the capacity to find subsurface imperfections without endangering the architectural stability of components. By using these techniques, industries can substantially extend the solution life of their devices, decreasing downtime and the associated financial problem of maintenance activities.
In addition, a durable welding assessment program sustains the optimization of maintenance timetables, shifting from reactive to anticipating maintenance methods. This proactive approach not just curtails unexpected failures yet likewise enhances source allowance, making sure that upkeep initiatives are concentrated and effective. Ultimately, the financial investment in strenuous welding examination is countered by the significant financial savings recognized via reduced maintenance needs, contributing favorably to the general functional performance of industrial ventures.
Improving Security Procedures
Although safety is a paramount issue in commercial operations, attaining site web optimum security criteria calls for a dedicated concentrate on the top quality and dependability of welded frameworks. Welding examination plays a vital role in this context, as it ensures that all joints and connections fulfill strict security standards. Comprehensive assessments help determine problems such as fractures, porosity, or insufficient blend that might compromise structural stability. Such problems, if left unaddressed, present considerable dangers, potentially leading to disastrous failures.
Methods like ultrasonic testing, radiographic screening, and magnetic bit assessment allow for in-depth his response assessment without damaging the structure. Implementing a durable high quality control system that consists of routine training for assessors and welders ensures adherence to developed safety criteria.
Last but not least, promoting a culture of security within the organization highlights the value of complete welding evaluations. Motivating open communication and partnership amongst welders, assessors, and engineers adds to a shared dedication to safety and security excellence. Welding Inspection Madison. In doing so, sectors can protect their procedures, protect employees, and preserve public trust fund

Verdict
Complete welding evaluation is essential in industrial applications, significantly boosting structural stability and reliability. Inevitably, the thorough implementation of welding examinations plays a crucial function in keeping operational effectiveness and safety in industrial setups.
As we explore the diverse benefits of thorough welding examinations, one have to take into consideration the broader effects on security, dependability, and cost-effectiveness in industrial operations.
The main goal of welding inspection is to guarantee that the welds are qualified of birthing the expected stresses and lots they will certainly encounter in solution. Reliable welding evaluation plays an indispensable role in get redirected here minimizing these expenses by making certain the stability and durability of welds, consequently reducing the threat of premature failings.Thorough welding assessment is important in commercial applications, substantially improving architectural integrity and integrity. Inevitably, the diligent implementation of welding evaluations plays an essential role in maintaining operational performance and security in industrial setups.
Report this page